The Role of Calibrated Equipment in Accurate Stack Monitoring
In today’s industrial landscape, the importance of environmental monitoring cannot be overstated. Industries must understand that The Role of Calibrated Equipment in Accurate Stack Monitoring is crucial for ensuring compliance with emission regulations.Governments, organizations, and environmental agencies are increasingly focused on ensuring that industries meet regulatory standards for air emissions, particularly from stacks and chimneys that release gases into the atmosphere. Accurate stack monitoring is a critical component in this process, allowing industries to assess the quantity and quality of emissions, and ensure they are within permissible limits. Central to achieving accurate stack monitoring is the use of calibrated equipment. Without properly calibrated instruments, data can be inaccurate, misleading, and ultimately, environmentally and economically harmful.
This article explores the pivotal role that calibrated equipment plays in stack monitoring, the consequences of using uncalibrated equipment, and how proper calibration techniques contribute to the overall efficiency, compliance, and environmental responsibility of industrial operations.
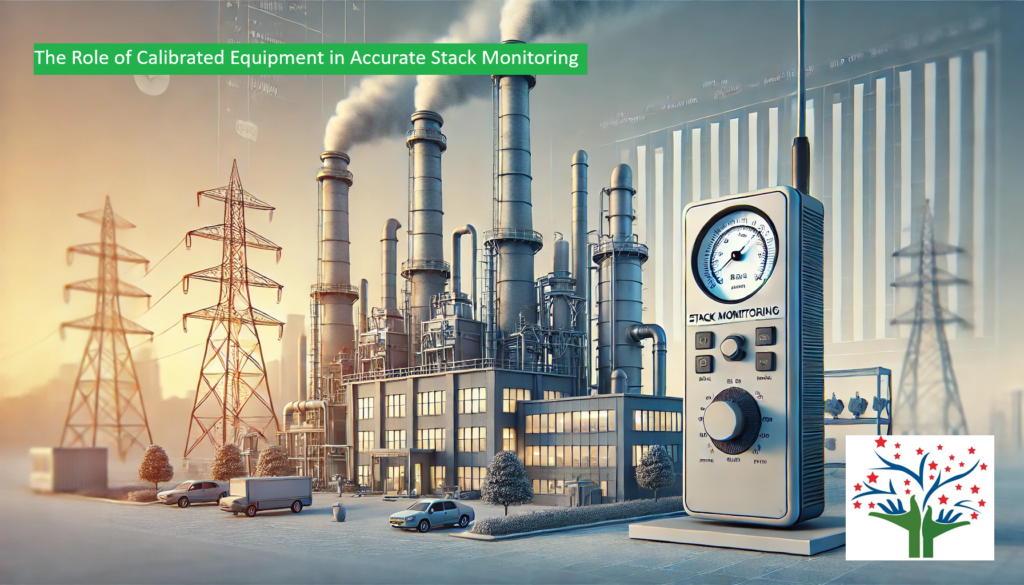
What Is Stack Monitoring?
Stack monitoring involves measuring the pollutants emitted from industrial stacks, chimneys, and vents. These pollutants include gases such as carbon dioxide (CO₂), sulfur dioxide (SO₂), nitrogen oxides (NOₓ), particulate matter, and volatile organic compounds (VOCs). The emissions are typically a byproduct of combustion processes, chemical reactions, or manufacturing activities. Stack monitoring is essential for determining whether a facility complies with environmental regulations set by authorities such as the Environmental Protection Agency (EPA) or local governing bodies.
The stack monitoring process typically involves sampling emissions using specialized equipment, analyzing the composition of gases and particles, and reporting the results. This data is used by industries to control emissions, make adjustments to processes, and demonstrate compliance with regulatory standards.
Read more about CPCB Guidelines for Stack Monitoring
Why Calibration Is Crucial in Stack Monitoring
The accuracy of stack monitoring results hinges on the equipment used to measure emissions. Calibration refers to the process of comparing the readings of an instrument to a known standard or reference value. Over time, environmental factors, mechanical wear, and usage can cause instruments to drift or deviate from their original accuracy. Regular calibration ensures that instruments provide precise and reliable data. The Role of Calibrated Equipment in Accurate Stack Monitoring cannot be overstated when it comes to maintaining environmental standards
Learn more about Stack Emission Monitoring Kit
In the context of stack monitoring, calibration is essential for several reasons:
- Regulatory Compliance: Most environmental agencies mandate the use of calibrated equipment for emissions monitoring. Calibration records are often required as part of the compliance documentation submitted to regulatory bodies. Failing to use calibrated instruments can lead to fines, penalties, or even the shutdown of industrial operations.
- Accuracy and Precision: Inaccurate data can have serious consequences. Overestimating emissions may result in unnecessary costs for pollution control, while underestimating emissions can lead to environmental harm and non-compliance. Calibrated equipment ensures that readings are accurate, reducing the risk of erroneous data.
- Data Integrity: Reliable data is crucial for making informed decisions about process optimization and environmental performance. Calibrated equipment provides the confidence that the data collected is trustworthy, forming the basis for any corrective actions or process improvements.
- Reputation and Credibility: Industries that consistently monitor their emissions with calibrated equipment build a reputation for environmental responsibility. This can lead to improved relationships with regulatory bodies, customers, and the community. Conversely, the use of uncalibrated or inaccurate equipment can damage a company’s reputation if it results in non-compliance or environmental harm.
Read more about Stack Emission Monitoring Procedure
Types of Equipment Used in Stack Monitoring
There are various types of equipment used in stack monitoring, each of which requires regular calibration to ensure accuracy. Some of the most commonly used instruments include:
- Gas Analyzers: These devices measure the concentration of specific gases such as CO₂, SO₂, NOₓ, and O₂. Gas analyzers rely on various detection principles such as infrared absorption, chemiluminescence, or electrochemical sensors, all of which must be calibrated regularly to maintain accuracy.
- Flow Meters: Flow meters measure the velocity and volume of gases passing through the stack. Accurate flow measurement is critical for calculating total emissions over time. Flow meters must be calibrated to account for changes in pressure, temperature, and gas composition.
- Particulate Matter Samplers: These instruments collect and measure the concentration of fine particulate matter (PM10 or PM2.5) in the emissions. Accurate measurement of particulate matter requires calibration of both the sampling device and the weighing equipment used to analyze the samples.
- Continuous Emission Monitoring Systems (CEMS): CEMS are automated systems that continuously monitor gas concentrations and flow rates. These systems are commonly used in power plants and large industrial facilities. CEMS require routine calibration using certified gas standards to ensure ongoing accuracy.
- Opacity Meters: Opacity meters measure the amount of light blocked by particulate matter in the emissions, providing an indirect measure of particulate concentration. Calibration ensures that opacity readings accurately reflect particulate levels.
Read about Stack Emission Monitoring & Testing
The Calibration Process
The calibration process typically involves comparing the instrument’s readings to a known reference standard, such as a certified gas mixture or a flow standard. Calibration can be done on-site (in-field) or in a controlled laboratory setting, depending on the type of equipment and the calibration requirements.
For stack monitoring equipment, calibration generally follows these steps:
- Pre-Calibration Check: Before beginning the calibration, a pre-check is often conducted to assess the current accuracy of the instrument. This may involve comparing the instrument’s readings to the expected values or using a calibration gas.
- Calibration Adjustment: If the instrument is found to be out of calibration, adjustments are made to bring it back into line with the reference standard. For example, if a gas analyzer is reading higher than the actual concentration of the calibration gas, the sensitivity may be adjusted to match the true concentration.
- Post-Calibration Verification: After calibration adjustments are made, the instrument is re-checked to verify that it is now reading accurately. This step ensures that the calibration was successful and that the instrument is ready for use.
- Documentation: Calibration results are documented and stored, either in the instrument’s memory or in external records. These records are essential for demonstrating compliance with regulatory requirements and for future reference.
- Routine Calibration Schedule: Most equipment manufacturers recommend a routine calibration schedule, often based on the number of operating hours, frequency of use, or the environmental conditions in which the instrument operates.
Importance of Stack Emission Monitoring & Testing
Consequences of Using Uncalibrated Equipment
Using uncalibrated equipment in stack monitoring can have several negative consequences:
- Non-Compliance with Regulations: Many environmental regulations require the use of calibrated equipment for stack monitoring. If a company fails to provide proof of calibration, it may face fines, penalties, or legal action from regulatory agencies.
- Inaccurate Emission Data: Uncalibrated equipment can produce inaccurate data, leading to underestimation or overestimation of emissions. This can result in unnecessary costs for pollution control measures or environmental damage due to excess emissions.
- Increased Operational Costs: If inaccurate data leads to over-reporting of emissions, a company may invest in unnecessary pollution control technologies or pay excessive emissions fees.
- Damage to Reputation: Industries that fail to monitor their emissions accurately may face public backlash, loss of business, and reputational harm. Environmental compliance is increasingly important to consumers and stakeholders, and companies that fail to meet standards can suffer significant consequences.
Best Practices for Ensuring Accurate Stack Monitoring
To ensure accurate stack monitoring, industries should follow several best practices related to equipment calibration:
- Use Certified Reference Standards: Always use certified reference materials or gas standards for calibration. These standards are traceable to national or international metrology institutes, ensuring that calibration is accurate and reliable.
- Follow Manufacturer Guidelines: Adhere to the equipment manufacturer’s recommendations for calibration frequency and procedures. This ensures that instruments are maintained in optimal condition and continue to provide accurate readings.
- Implement a Calibration Management System: A calibration management system can help track the calibration history of each instrument, schedule future calibrations, and maintain records for regulatory compliance.
- Conduct Regular Audits: Periodically audit the calibration process to ensure that all equipment is being calibrated properly and according to schedule. Audits can help identify any gaps or areas for improvement in the calibration process.
- Train Personnel: Ensure that personnel responsible for stack monitoring and equipment calibration are adequately trained. Properly trained staff can perform calibrations more accurately and identify potential issues before they affect data quality.
Conclusion
Calibrated equipment is the backbone of accurate stack monitoring. Without proper calibration, emissions data can be unreliable, leading to regulatory non-compliance, environmental harm, and increased operational costs. Regular calibration ensures that monitoring equipment provides precise, trustworthy data that forms the foundation for effective environmental management and regulatory compliance.By recognizing The Role of Calibrated Equipment in Accurate Stack Monitoring, companies can enhance the precision of their emissions data and contribute to environmental sustainability.
Industries that prioritize calibration and follow best practices for stack monitoring not only meet regulatory requirements but also contribute to the global effort to reduce air pollution and protect the environment. As the world moves toward stricter environmental standards, the role of calibrated equipment in stack monitoring will continue to be critical for achieving sustainable industrial operations.
The purpose of calibrating equipment is to ensure that it provides accurate and reliable measurements by comparing its readings to known standards, which helps maintain precision and compliance with regulatory requirements.
Calibrating equipment improves accuracy by adjusting the instrument’s measurements to match a known standard, correcting any deviations or errors, and ensuring consistent, precise data over time.
Accurately calibrated instruments are important because they ensure reliable measurements, which are critical for regulatory compliance, process optimization, and environmental protection. Without accurate calibration, data can be misleading, leading to potential fines, operational inefficiencies, or environmental harm.
It is important to have calibrated and synchronized navigational equipment to ensure accurate positioning, timing, and direction, which are essential for safe and efficient travel. Without proper calibration and synchronization, navigational errors can occur, leading to potential safety risks, misrouting, or operational inefficiencies.
Calibration is the process of adjusting and verifying the accuracy of an instrument or device by comparing its measurements to a known standard. The purpose of calibration is to ensure that the device provides accurate and reliable results, improving measurement precision and ensuring consistency in performance, which is crucial for compliance, safety, and operational efficiency across various fields.
If equipment is not calibrated, it can produce inaccurate or unreliable measurements, leading to errors in data, non-compliance with regulations, safety risks, and potential damage to processes or products. Inaccurate equipment may also result in increased operational costs, inefficiencies, and compromised decision-making based on faulty data.
Calibrated accuracy refers to the level of precision and reliability an instrument achieves after being adjusted through calibration. It indicates how closely the instrument’s measurements match the true or standard values, ensuring that the device provides accurate data within specified tolerances after calibration.
To improve calibration accuracy, use certified reference standards, conduct calibrations in controlled environments, and follow regular calibration schedules. Ensuring trained personnel and maintaining precise records also contribute to consistent and accurate results.
To check when equipment was last calibrated, review the calibration certificate or log, which should include the calibration date, the next due date, and details of the calibration process. Many instruments also display calibration status or dates on labels or digital interfaces.
The scope of calibration refers to the range of measurements, conditions, and parameters for which an instrument is tested and adjusted during the calibration process. It includes the types of measurements being calibrated (e.g., temperature, pressure, flow), the accuracy required, and the specific operating conditions or standards used to ensure the equipment performs correctly within its intended use.
Equipment should be calibrated based on the manufacturer’s recommendations, regulatory requirements, usage frequency, and environmental conditions. Typically, calibration is done annually, but more frequent calibration may be required for high-precision equipment or instruments used in critical environments.
Calibrated equipment is used to ensure accurate, reliable measurements in various applications, such as manufacturing, laboratory testing, environmental monitoring, and quality control. It helps maintain compliance with standards, improve process efficiency, and ensure safety and accuracy in operations.
Calibration primarily improves accuracy by adjusting an instrument to ensure its measurements align with known standards. While calibration enhances accuracy, it does not directly improve precision, which refers to the consistency of repeated measurements. However, accurate instruments can help ensure reliable and consistent data over time.
The calibration process involves comparing an instrument’s measurements to known standards, adjusting if needed, and verifying accuracy, followed by documentation and labeling. This ensures the equipment provides reliable, accurate data for future use.