Stack Emission Monitoring Procedure
Stack Emission monitoring procedure includes tasks of Measurement, testing, sampling and analysis. Onsite determination of physical parameters of flue gases such as temperature, flow and pressure also involved in Stack emission monitoring.
Air Quality is a major environmental responsibility for all manufacturing industries. Those industries can use air quality monitoring or stack monitoring to measure the degree of pollutants or contaminants present in the current exhaust air and take the required steps to reduce them.
All industries must have a sampling port built into their stack and a permanent sampling platform to ease the Stack Emission Monitoring Procedure for environmental consultants who perform monitoring of stack emission.
Purpose of Stack Emission Monitoring
The primary purpose of stack emission monitoring is to:
- Ensure regulatory compliance: Most countries have stringent environmental regulations in place to control industrial emissions. Regular monitoring ensures that industries comply with these standards.
- Reduce environmental impact: By measuring pollutants released into the air, industries can take corrective measures to minimize their environmental footprint.
- Promote public health and safety: Harmful gases such as SO₂, NOx, and PM can have serious health impacts on nearby communities. Monitoring emissions helps in reducing these risks.
- Facilitate operational efficiency: Monitoring can identify inefficiencies in processes, allowing industries to make adjustments that reduce emissions and improve performance.
Key Pollutants Monitored in Stack Emissions
There are several common pollutants that are regularly monitored in stack emissions:
- Particulate Matter (PM): Fine particles, often from burning fuels or industrial processes, can penetrate the respiratory system, causing health issues.
- Sulfur Dioxide (SO₂): This gas is primarily emitted from the combustion of fossil fuels. It can lead to acid rain and respiratory issues.
- Nitrogen Oxides (NOx): NOx gases are produced during combustion and contribute to smog formation and respiratory problems.
- Carbon Monoxide (CO): Produced by incomplete combustion of carbon-based fuels, CO is harmful when inhaled and contributes to air pollution.
- Volatile Organic Compounds (VOCs): These organic chemicals evaporate easily and contribute to air pollution and smog formation.
- Greenhouse Gases (GHGs): CO₂, CH₄, and other greenhouse gases trap heat in the atmosphere, contributing to global climate change.
Read More about Stack Emission Monitoring
Stack Emission Monitoring Procedure
Selection of Sampling Site in Stack Emission Monitoring Procedure
The objective of sampling in the Stack Emission Monitoring Procedure is to determine the accurate degree of pollutants present in the air emitted from the stack. Laminar flow should be present in the stack to get accurate readings.
Stack identification: The specific stack to be monitored must be identified. This usually involves studying the industrial process to determine which stack is responsible for significant emissions.
Sampling location: Choose a location on the stack that is accessible and provides representative samples. The location should be far enough from bends or obstructions to avoid turbulence that could affect the sample.
Equipment setup: Install the necessary monitoring equipment, such as sampling probes, analyzers, and flow meters, at the chosen location.
To select a representative sample sampling point should be at least eight stack diameter downstream and two-stack diameter upstream from any joint, bend, expansion and contraction.
Also Read How to calculate DG or Boiler Stack Height as per CPCB Guidelines
Traverse Points
As per new Notifications, all stacks must have a sampling post and sampling platform. The location of traverse points will be decided by the pollution control board.
After previous criteria met, to determine the minimum traverse points required the first diameter of the stack is to be calculated in the case of a circular stack. Also, it should be far 3cm from the stack wall.
Know more about how to select Traverse Point in stack monitoring
Stack Emission Monitoring Procedure Download files (PPT and PDF)
You can download Stack Emission Monitoring Procedure files from here:
Molecular Weight Determination
Molecular weight can be found by drawing a known amount of gas into a gas chromatograph or Orsat apparatus. Moisture should be found. Molecular weight can be calculated by knowing gas components.
The average molecular weight can be determined by using the below-mentioned formula:
M = ∑ (i=1)^n (xi Mi)
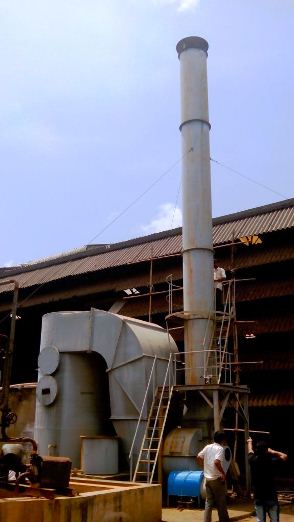
X is the mole fraction and Mi is mole weight of each constituent in a mixture of a several constituent.
Velocity Determination
Once the Pitot tube is connected Dynamic and static pressure is found using a manometer. Also, the Temperature inside the duct is measured. The velocity of gas and amount of air can be found using the formula
Learn the Advantages of Stack Emission testing
You can also use our stack monitoring calculators to calculate the velocity of gases online.
Moisture Determination
Moisture can be determined by dry and wet bulb temperature and the referring to the psychometric chart. Also, the condenser method works well for almost all gas streams and comparatively easy to perform.
Condenser Method to determine Moisture in a Gas Dtream
In this process sample of the stack is extracted through a filter to remove particulate matter than through the condenser, collecting the condensate formed in the process and then it is measured.
Wet/Dry Method to Determine Moisture in Gas Stream
The equilibrium temperature attained by water which is vaporizing into a gas of constant composition and the constant dry bulb is called wet-bulb temperature. The amount of depression of wet bulb temperature below the dry bulb is the saturation degree of humidity of the gas. Hence, the moisture content of gas can be determined by using the wet and dry bulb method.
Sample Recovery
After the sample has cooled, brush down the dust on side of the nozzle into a thimble and replace it in a labelled container.
Sampling and Analysis
- Isokinetic sampling: For particulate matter, carefully insert the sampling probe into the stack at the desired location. Maintain the same velocity between the gas in the stack and the sample being drawn to ensure accurate results.
- Gas sampling: For gases like SO₂ and NOx, a non-isokinetic method is used, where gas is drawn into a collection device, often through an impinger or filter.
- Sample preservation: Once the samples are collected, preserve them carefully for laboratory analysis. For gases, ensure that the sample bottles are sealed properly, and for particulate matter, store the filters in a clean environment to avoid contamination.
- Laboratory analysis: Transport the samples to a laboratory for detailed analysis. The lab will use a variety of techniques, such as gas chromatography or mass spectrometry, to identify and quantify the pollutants in the sample.
Reporting and Documentation
- Data analysis: Analyze the data to calculate the concentration of pollutants and compare it to regulatory limits. This involves using mathematical equations to account for variables such as gas flow rate, stack temperature, and pressure.
- Reporting: Prepare a detailed report for regulatory authorities, which includes the methods used, results, calibration data, and any deviations or abnormalities during the sampling process.
- Record-keeping: Maintain a log of the monitoring results for future reference. This is important for auditing and ensuring long-term compliance.
Read more about CPCB Guidelines for Stack Monitoring
Stack emission monitoring is an essential process for ensuring that industrial emissions are within acceptable limits and do not pose a threat to the environment or public health. Whether through continuous systems like CEMS or manual sampling techniques, industries must adhere to rigorous procedures to measure and control pollutants. By following the correct methodologies, calibrating equipment properly, and accurately analyzing data, industries can reduce their environmental impact and ensure compliance with local and international regulations.
This blog is written by Perfect Pollucon Services. They offerEnvironmental services in India including Consultancy and Monitoring Services.
The key parameters for stack emission monitoring include Particulate Matter (PM), Sulfur Dioxide (SO₂), Nitrogen Oxides (NOx), Carbon Monoxide (CO), Oxygen (O₂), and Carbon Dioxide (CO₂). Additional pollutants such as Volatile Organic Compounds (VOCs) and Heavy Metals (e.g., Mercury, Lead) may also be monitored based on regulatory requirements.
Stack emission refers to the release of combustion gases and particulate matter from industrial sources like boilers, furnaces, and diesel generators through a chimney or stack. These emissions are monitored and regulated to ensure compliance with environmental standards.
The Central Pollution Control Board (CPCB) prescribes standards for various industries based on emission limits for pollutants such as PM, SO₂, and NOx. CPCB also provides guidelines on the frequency, methodology, and permissible limits for stack emissions.
Stack gas measurement is typically conducted using isokinetic sampling, continuous emission monitoring systems (CEMS), or grab sampling methods. Instruments such as gas analyzers and particulate samplers are used to quantify pollutants.
Stack emission limits vary by industry and fuel type but typically include PM < 50 mg/Nm³, SO₂ < 100 mg/Nm³, and NOx < 600 mg/Nm³ for industrial boilers, as per CPCB norms.
For most industries, CPCB limits NOx emissions to 450–600 mg/Nm³, while stricter standards apply to newer installations.
A stack test is an official performance assessment of an industrial emission source, conducted using standard methods to determine pollutant levels in exhaust gases.
Hi ,
Basically we are a Environmental consultants based in UAE. We have some projects as Stack/Soil/Noise air monitoring in Saudi,Oman&Abudhabi with our clients.we are looking for a subcontract team to do this projects.
We required your service team to do the work completion for different projects based in Middleast.if your company have interest with those projects please revert back soon.
Thank you for your Inquiry but Unfortunately we don’t offer services outside India. 🙂
Please can we team up for Environmental projects in Africa or West Africa?
NEMAS Consult Limited has well equipped environmental monitoring equipment and qualified personnel’s to carry out any environmental projects
Sure,
You can call us on +91-9930180059 for more information.