ASTM B117
Corrosion is an age-old challenge that industries and manufacturers have constantly grappled with. The destructive impact of corrosion can lead to significant economic losses, safety hazards, and environmental issues. To combat this, various methods and standards have been developed to assess the corrosion resistance of materials and coatings used in different applications. One such method is the ASTM B117 salt spray test, which has become a widely accepted and standardized technique to evaluate a material’s corrosion resistance.
In this article, we will delve into the details of ASTM B117, its significance, procedure, limitations, and its broader applications in ensuring the durability of materials.
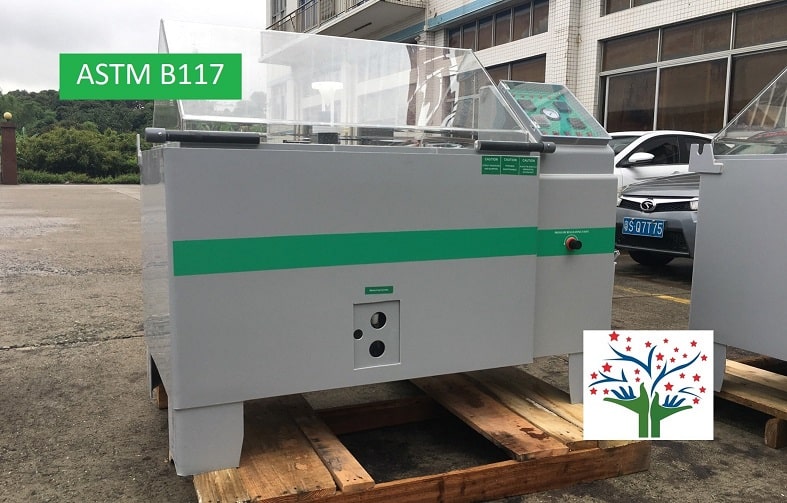
“https://www.wewontech.com/ct-160d-salt-spray-chamber”
What is ASTM B117?
ASTM B117 is a test method established by the American Society for Testing and Materials (ASTM) to simulate and evaluate the performance of materials, coatings, and surfaces under corrosive conditions.
The test subjects the materials to a controlled saline environment, replicating the harsh conditions they may face in real-world applications. This controlled environment consists of a continuous spray of a salt solution onto the specimen, imitating the effects of natural salt-laden atmospheres or other corrosive environments.
Significance and Objectives of ASTM B117
The primary objective of the ASTM B117 salt spray test is to determine the corrosion resistance of a material or coating over a specified period. The test provides valuable data on how a material will perform in corrosive conditions, helping manufacturers and engineers make informed decisions about material selection and design considerations.
By evaluating corrosion resistance, it becomes possible to improve the longevity and reliability of products, reduce maintenance costs, and enhance safety, especially in industries such as automotive, aerospace, marine, and construction.
The Salt Spray Test Procedure
The ASTM B117 standard specifies a comprehensive procedure to conduct the salt spray test. Here is a general overview of the key steps involved:
- Sample Preparation
Before the test, the samples, often in the form of panels or coated components, are carefully cleaned and degreased to remove any contaminants that might interfere with the test results. The samples are then dried thoroughly to ensure a consistent starting point for the test.
- Test Chamber Setup
The test is carried out in a controlled environment called the salt spray chamber. The chamber typically consists of a salt solution reservoir, atomizing nozzles, and a test rack to hold the samples. The salt solution is prepared according to the ASTM B117 specifications, typically using sodium chloride (NaCl) dissolved in deionized water.
- Exposure to Salt Spray
The prepared samples are mounted on the test rack inside the salt spray chamber. The chamber is sealed, and the salt solution is atomized into a fine mist, creating a continuous spray that envelopes the samples. The mist is dispersed uniformly to ensure even exposure.
- Test Duration (ASTM B117 Salt Spray Test Hours)
The duration of the salt spray test can vary depending on the material, coating, or industry requirements. Common test durations range from 24 hours to over 1000 hours. Shorter test durations are often used for initial screening, while longer durations such as such as 500 to 1000 hours or more, provide a more rigorous assessment of corrosion resistance.
Manufacturers and engineers choose the appropriate test duration based on the expected real-world exposure conditions and the desired level of confidence in the material’s ability to withstand corrosive environments. Longer test periods are particularly useful for applications where extended durability and resistance to corrosion are critical, such as in automotive, aerospace, marine, and construction industries.
- Evaluation
After the test period elapses, the samples are removed from the chamber, cleaned to remove any remaining salt residues, and examined for signs of corrosion. Evaluation can include visual inspection, microscopy, weight loss measurement, and various other methods to determine the extent of corrosion.
Read more about Corrosion Testing Methods
Limitations of the Salt Spray Test:
While the ASTM B117 salt spray test is a valuable tool for evaluating corrosion resistance, it is essential to understand its limitations to interpret the results correctly. Some of the key limitations include:
Idealized Conditions
The test is a controlled simulation of corrosive conditions and may not fully replicate the complexity of real-world environments. Different environmental factors like temperature, humidity, and pollutants may significantly affect corrosion behavior but are not accounted for in the test.
Different Corrosion Types
The test primarily assesses general corrosion and may not effectively simulate other corrosion types like pitting corrosion, crevice corrosion, or stress corrosion cracking. These corrosion mechanisms might be more relevant for specific applications.
Coating Thickness
The test assumes a uniform coating thickness, but in practical applications, coating thickness can vary, leading to different corrosion performance.
Lack of Mechanical Stresses
The test does not incorporate mechanical stresses, which can influence corrosion behavior in real-world scenarios.
Read more about Corrosion Testing Labs
Applications of ASTM B117
ASTM B117 is widely used across various industries to assess corrosion resistance, but some industries find it particularly valuable:
- Automotive Industry: Automotive components, especially those exposed to road salts and environmental elements, undergo salt spray testing to ensure they meet corrosion resistance standards.
- Aerospace Industry: Aircraft parts and components must withstand harsh environmental conditions, including exposure to salt in coastal and high-humidity areas.
- Marine Industry: Shipbuilding and maritime equipment are often subjected to saltwater environments, necessitating corrosion-resistant materials.
- Coating Manufacturers: Companies that produce protective coatings, paints, and surface treatments use salt spray testing to develop and improve their products.
- Research and Development: Researchers use the ASTM B117 test to study the corrosion performance of new materials and coatings.
Read more about Corrosion Testing at Data Centre
ASTM B117 Standard
ASTM B117 is a widely recognized and utilized standard established by the American Society for Testing and Materials (ASTM) to assess the corrosion resistance of materials and coatings. It involves subjecting samples to a controlled salt spray environment to simulate the effects of corrosive conditions they may encounter in real-world applications.
The test duration typically ranges from 24 hours to over 1000 hours, with the results providing valuable data for manufacturers and engineers to make informed decisions on material selection and design considerations, ensuring the durability and reliability of products in various industries, including automotive, aerospace, marine, and construction.
ASTM B117 Salt Spray Test Acceptance Criteria
The acceptance criteria for the ASTM B117 salt spray test are not specified within the standard itself. Instead, they are typically determined by the relevant industry standards, product specifications, or customer requirements. The criteria vary based on the type of material or coating being tested and the intended application.
Common acceptance criteria may involve evaluating the extent of corrosion, appearance of specific corrosion types, or performance indicators such as blistering or delamination. Manufacturers and engineers must refer to applicable industry or customer-specific standards to define the acceptable levels of corrosion for their materials and coatings.
Perfect Pollucon Services offers Corrosion Testing Services using advanced methodologies and equipment to evaluate the corrosion resistance of materials and products, enabling industries to make informed decisions regarding material selection and protective measures for enhanced durability and performance.
ASTM B117 Final Thoughts
Corrosion remains a persistent challenge for industries worldwide, but standardized test methods like ASTM B117 provide valuable insights into the corrosion resistance of materials and coatings. By subjecting samples to controlled salt spray conditions, engineers and manufacturers can better predict a material’s behavior in corrosive environments.
While the test has its limitations, it serves as an essential tool in the ongoing quest for more durable, safer, and longer-lasting products. As industries continue to evolve, the ASTM B117 salt spray test will remain a crucial pillar in ensuring materials’ reliability and performance in corrosive environments.
Frequently Asked Questions:
The title of ASTM B117 is “Standard Practice for Operating Salt Spray (Fog) Apparatus.”
ASTM B117 and ASTM G85 are both corrosion testing standards developed by ASTM, but they differ in their scope and focus. ASTM B117 is a specific standard that outlines the procedures for conducting the salt spray test, which simulates corrosive conditions caused by salt-laden atmospheres.
It primarily evaluates the general corrosion resistance of materials and coatings. On the other hand, ASTM G85 encompasses several test methods, each designed to simulate specific corrosive environments, such as acetic acid salt spray or seawater acidified conditions, and is more versatile in assessing different types of corrosion mechanisms.
The selection between ASTM B117 and ASTM G85 depends on the specific corrosion type and real-world application being considered.
ASTM B117 and JIS Z2371 are both standards used to assess the corrosion resistance of materials and coatings, specifically through the salt spray test. The main difference lies in their origin and geographical application.
ASTM B117 is an American standard developed by the American Society for Testing and Materials (ASTM), while JIS Z2371 is a Japanese standard established by the Japanese Industrial Standards (JIS). Despite the differences in origin, both standards serve similar purposes and follow similar principles for conducting the salt spray test.
ASTM (American Society for Testing and Materials) and ISO (International Organization for Standardization) are two prominent organizations that develop technical standards for various industries. While ASTM primarily focuses on standards relevant to industries within the United States, ISO standards have international relevance and are adopted by countries worldwide.
ASTM covers a wide range of industries and has over 12,000 standards, whereas ISO develops standards for almost all sectors and has over 23,000 international standards.
Both organizations use different naming conventions for their standards, and while ASTM standards are widely used and respected globally, ISO standards are the most widely accepted and implemented global standards.
ASTM B633 and ASTM A153 are two distinct ASTM standards that pertain to different aspects of metal coatings:
ASTM B633: This standard specifies the requirements for electrodeposited coatings of zinc on iron and steel substrates, known as zinc plating or electroplating. The coatings can vary in thickness and provide corrosion protection and a decorative appearance.
ASTM A153: This standard covers the requirements for hot-dip galvanizing of iron and steel products. Hot-dip galvanizing involves immersing the steel components in a bath of molten zinc, creating a thick, durable coating that provides excellent corrosion resistance.
In summary, ASTM B633 deals with electroplating zinc onto iron and steel, while ASTM A153 deals with the hot-dip galvanizing process to provide a zinc coating on iron and steel products. Each standard serves specific applications and offers different characteristics in terms of coating thickness, corrosion protection, and method of application.